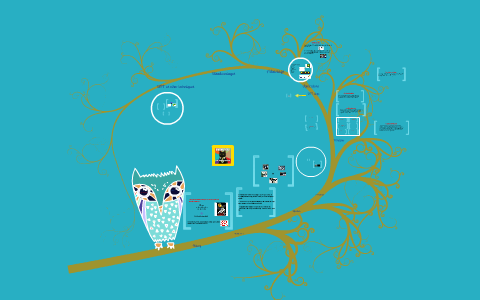
In today’s competitive manufacturing landscape, companies are striving to enhance their production processes to meet customer demand more effectively. One of the most innovative approaches to achieving this goal is Demand Flow Technology (DFT). This methodology is reshaping industries by optimizing production flows, minimizing waste, and ensuring that manufacturing aligns with real-time customer demand. In this comprehensive guide, we explore Demand Flow Technology, its principles, applications, and why it’s crucial for modern businesses.
What is Demand Flow Technology?
Demand Flow Technology (DFT) is an advanced manufacturing strategy designed to streamline production systems by synchronizing them with actual customer demand. Unlike traditional methods that rely on forecast-driven production (known as “push” manufacturing), DFT adopts a “pull” system where goods are produced based on real-time orders, ensuring efficient resource use and reducing excess inventory.
At its core, DFT aims to eliminate inefficiencies within manufacturing processes. By focusing on real demand rather than speculative projections, it ensures a continuous and balanced flow of products through production lines, creating an agile, adaptive manufacturing system.
The Principles of Demand Flow Technology
1. Flow Management
Effective flow management is the cornerstone of DFT. It involves mapping every step of the manufacturing process to identify and eliminate bottlenecks that slow down production. This step-by-step analysis helps businesses streamline operations, ensuring that each phase operates as smoothly as possible.
2. Demand-Pull System
DFT operates on the demand-pull principle, where production is directly influenced by actual customer orders rather than predictive forecasting. This method prevents overproduction and ensures that resources are only used to meet immediate needs, which results in a more efficient and cost-effective manufacturing process.
3. Flexibility and Adaptability
One of the defining characteristics of DFT is its flexibility. Companies must be able to adjust production lines quickly to accommodate changes in customer demand. This requires having the capability to perform quick changeovers and adjust production volumes in response to fluctuations in demand. Shorter production runs and adaptable equipment are key components of this flexible approach.
Benefits of Demand Flow Technology
1. Enhanced Efficiency
By aligning production schedules with actual demand, DFT significantly reduces waste and optimizes resource allocation. This approach helps manufacturers avoid overstocking and understocking, allowing them to streamline their processes. DFT creates a continuous flow that eliminates idle time and maximizes throughput.
2. Cost Reduction
With the demand-pull system, businesses avoid the high costs of overproduction and excess inventory. Rather than spending resources on storing unsold products or disposing of obsolete stock, DFT enables a just-in-time production approach, where inventory levels are optimized, leading to substantial cost savings.
3. Improved Customer Satisfaction
Since DFT ensures that products are made to meet current demand, it reduces lead times and allows companies to fulfill orders more quickly. In industries where customer expectations for speed and customization are high, DFT helps companies stay ahead of the competition by offering faster turnaround times and greater product availability.
4. Scalability and Sustainability
Demand Flow Technology is scalable, making it an attractive solution for companies of all sizes. From large corporations to smaller startups, businesses can adapt DFT principles to suit their specific operational needs. Moreover, DFT contributes to sustainability by reducing waste and energy consumption, making it a valuable strategy for environmentally-conscious companies.
Real-World Applications of Demand Flow Technology
Automotive Industry
In the automotive sector, Toyota is a prime example of a company that has successfully implemented DFT. By manufacturing vehicles based on actual customer orders, Toyota minimizes overproduction and ensures that its cars match consumer preferences. This lean approach to production allows for a more efficient supply chain and a reduction in inventory costs.
Electronics Sector
Dell has adopted DFT to create custom-built computers according to specific customer orders. This demand-driven production method ensures that each product is tailored to individual specifications, improving both customer satisfaction and operational efficiency. As demand for customization grows, this method provides a significant advantage over traditional mass-production models.
Consumer Goods
For companies in the consumer goods industry, Procter & Gamble utilizes Demand Flow Technology to adjust production based on real-time demand, enabling them to respond swiftly to shifts in consumer preferences. This agility helps P&G maintain optimal stock levels, ensuring that products are always available on store shelves, reducing both overproduction and stockouts.
How Does Demand Flow Technology Compare to Traditional Manufacturing?
In traditional manufacturing, production is often driven by forecasts and predictive models. These forecasts can be inaccurate, leading to overproduction or underproduction. DFT, on the other hand, focuses on real-time data, adjusting production dynamically to align with actual market demand.
Traditional systems tend to accumulate excess inventory, increasing storage costs and tying up valuable resources. DFT’s lean approach minimizes this risk by only producing goods when necessary. Furthermore, traditional methods often lack the adaptability required to respond to rapid market changes, whereas DFT thrives on flexibility and quick adjustments.
Challenges in Implementing Demand Flow Technology
While the benefits of DFT are clear, there are challenges associated with its implementation. One of the primary obstacles is the cultural shift required within the organization. Employees must embrace a demand-driven mindset, and machinery must be adapted to accommodate the flexibility needed for rapid changeovers.
Additionally, investing in technology and infrastructure to support DFT can be costly. However, these investments often pay off in the long term through enhanced efficiency, reduced waste, and improved customer satisfaction.
Integrating DFT with Other Manufacturing Methodologies
DFT is not a standalone solution; it can be integrated with other methodologies to maximize efficiency. For instance, combining DFT with Lean Manufacturing can help further eliminate waste and optimize workflows. Additionally, integrating Six Sigma with DFT can improve quality control and reduce defects in the production process.
The integration of DFT with these methodologies creates a hybrid system that allows businesses to adapt quickly to customer demands while maintaining high standards of quality and efficiency.
Future of Demand Flow Technology
As consumer demand continues to evolve and industries become more globalized, the need for efficient and flexible manufacturing systems will only increase. Demand Flow Technology is poised to play a central role in shaping the future of manufacturing. As technology advances, DFT will become even more refined, offering businesses the tools they need to stay competitive in a rapidly changing world.
In the future, automation and artificial intelligence will likely play an even greater role in optimizing demand flows. With the integration of these technologies, DFT will become more predictive and responsive, enabling businesses to anticipate customer needs with even greater precision.
Conclusion
Demand Flow Technology represents a transformative shift in manufacturing, offering businesses a more efficient, cost-effective, and responsive approach to production. By aligning production with actual customer demand, DFT not only reduces waste and optimizes resources but also improves customer satisfaction and supports sustainability efforts. Whether in the automotive, electronics, or consumer goods sectors, DFT is proving to be a vital strategy for modern manufacturers.
As industries continue to evolve, the adoption of Demand Flow Technology will be a key differentiator for companies looking to remain competitive in an increasingly fast-paced and customer-centric market. By embracing DFT, businesses can ensure that they are ready to meet the challenges of the future while delivering high-quality products that meet the demands of today’s consumers.